(Last updated April 7, 2020)
To all our customers, suppliers, employees, and contractors:
Quasonix remains dedicated to meeting the needs of our customers and ensuring the welfare of everyone we work with. Recognizing that the unprecedented global situation impacts every facet of our lives and our businesses, this status update is meant to share some insights, with the limited visibility we have today.
- The safety and long-term well-being of our employees is our first priority, and we will take steps to achieve that even if it delays our deliveries. In adhering to guidance provided by the US Centers for Disease Control (CDC), we are encouraging anyone who can work from home to do so, and we are providing relevant information and reminding employees to take all reasonable precautions to avoid spreading infection, whether inside or outside the office.
- Our labor force is currently at full strength, but the inefficiency of working in isolation (either working from home, or physically separated at the office) has begun to take its toll on our delivery schedules (details below).
- We are taking steps to minimize delays. Quasonix keeps safety stock on long-lead items and high-use parts, which allows us to maintain relatively short lead times to our customers. Despite this, isolated shortages have begun to appear, and this will undoubtedly continue through the next several months. We are actively developing alternate sources for any item where inventory levels are falling or expected to do so.
- Our production schedules are being monitored on a daily basis. The impact of personnel working in isolation and material shortages falls into roughly three groups:
- Small products (items carried in one hand). Our small products, such as transmitters, are generally ushered through manufacturing and test by no more than two or three people. Working in isolation from each other has a minimal impact on our production throughput, so we can sustain our typical production schedule, so long as material continues to be available. We currently have 492 transmitters on order, of which 8 are late on delivery. The 72 units due in April are low risk, but the risk of late delivery rises in the summer months, as material inventory may dwindle.
- Medium products (items carried in two hands). Receivers are a good example in this category. The manufacturing and test flow for these items involves 6 to 8 people, so working in isolation has significantly impacted our deliveries. We currently have 104 receivers, receiver analyzers, and status loggers on order, of which 21 are past due. Some of the 45 units due in April are at high risk and we are working with the customers for those units to arrange partial deliveries. If material holds up and our team stays healthy, we expect to be nearly back on schedule by mid-summer.
- Large systems (items we ship by freight carriers). Antenna systems are a good example in this category. Assembling and testing these large systems requires 20 to 30 people, all of whom need material at several levels of sub-assembly. The combination of material shortages and the inefficiency of working in isolation conditions virtually assures that all these systems will be delivered late. Of the 29 antenna systems currently on order, 16 are due this year. Nearly all of those will be late, probably by 3 to 4 months. We are exploring every avenue to improve the delivery schedules, but we will not put our people at risk by pretending that a group of 20 or more people is somehow “isolated.” We apologize in advance for any inconvenience caused by these late deliveries, but human resources are irreplaceable.
- We will continue to keep you informed. This report will be updated as there is additional information to share.
Best regards,
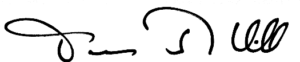
Terrance J. Hill, President